お手元で本コラムをご覧いただきたい方は、こちらからダウンロードいただけます。
第1回では事業別に収益管理が可能であるROIC(投下資本利益、Return on Invested Capital)を取り上げ、ROICの概要及び製造業においての活用のポイントについて述べてきました。経営と現場をぶつ切りにせず、繋がりを持ったROICからの課題・施策の展開が重要です。本コラムでは製造現場視点から生産特性を類別し、類別ごとのより具体的な課題の把握とソリューションの方向性について述べたいと思います。
1 生産の特性と類別
ROICの課題展開は売上向上、費用削減、資産効率化の3つの観点での展開となりますが、製造業の業種・業態により重点となる課題は異なります。そのため本コラムでは「品種・生産量」の大小と「製品形態」の2つの軸で類別し、類別したセグメントごとに課題を見ていきます(図表1)
国内製造業の主要領域である多品種少量を軸に素材産業系である「バッチプラント型」と機械等を想定とした「加工・組立系」の2つを対象とします。
図表1 「品種・生産量」と「製品形態」での製造業の類別
2 バッチプラント型の製造業における課題とソリューションの方向性
① 費用削減(製造原価率低減)に向けた課題とソリューションの方向性
製造原価は費目別に「単価低減」と「使用量削減」の観点で、課題とソリューションの方向性を展開できます。その中でも原材料費が最も多く、原材料費低減が重要課題となります(図表2)なお、図表2に費目別の構成比率を参考に示していますが、当然ながら個社により構成比率は異なるため、公開データに基づいた製造業の平均的な値と捉えていただけると幸いです。原価低減の方向性は「単価低減」と「使用量削減」の2つに分けられます。バッチプラント型の製造業は素材を取り扱う化学、医薬、食品業界とすると、原材料単価は市況で決まることが多く、その場合単価低減を個社のコントロールで行うことは難しいです。そのためここでは原材料の使用量削減の方向性について述べます。
図表2 製造原価の費目別改革の方向性
原材料の使用において製造工程で必ずロスが発生します。バッチプラント型製造業では原材料を配合、送液、反応、充填といった一連の工程がプラント内で行われ、見た目にはロスが見えなく、わかりづらい特徴があります。そのため製造フローと各工程でのロス発生箇所、ロスの区分、発生量をマップで可視化をすることが第一歩です(図表3)定量的に可視化した情報から改善対象の優先順位を定め、詳細のソリューションを実行していきます。
② 資産効率化(固定資産回転率向上)に向けた課題とソリューションの方向性
バッチプラント型の製造業の特性は、ものづくりは設備が主体であり、人は原材料の投入や設備の監視、切替などの補佐的な作業を行うことにあります。これらは図表2で示した製造原価のうち、労務費や設備費は固定費にあたるため、原材料費のように直接的に量や単価を削減することができません。ROICの3つの課題観点のうち、資産効率化にあたります。すなわち、「設備を最大限の稼動率で活用し、人は役割を定めて適正人数で配置した生産体制を整える」ことが課題となります。
設備稼動率を操業時間に対する稼動時間の割合とすると、設備稼動率の主な低下要因は計画ロス、切替ロス、設備故障ロスの3つが挙げられます(図表4)計画ロスと切替ロスは発生する要因が生産計画で決められる品種の生産順序にあり、改善余地はありますが顧客からの受注状況に左右されてしまいます。設備故障ロスは、根本原因が製造現場での設備保全の良し悪しであるため、ここでは設備故障ロスを重点課題として、ソリューションの方向性を述べます。
設備故障ロスのソリューションは「予防保全」の体制を整えることにあります。設備保全はトラブルが発生してから対処する「事後保全」とトラブルを未然に防止するための「予防保全」に分けられます。当然ながら設備故障ロスを低減するには予防保全が重要です。予防保全の活動はさらに「製造現場主体の自主保全活動」と「保全部門主体の専門保全活動」に分けられます。定義、特徴、実施ステップの詳細は図表5に整理して示しておりますが、これらの活動をうまく機能させるポイントは製造現場と保全部門がお互い連携することにあります。そのためには狙いとお互いの部門の役割を明確にした活動とすることが重要です。直接的な効果は設備稼動率の向上ですが、自主保全と専門保全の活動を機能させ、継続することが人の考え方や行動を変え、人を育てることに繋がります。人が育てば現場は強くなります。このことが予防保全活動の真の成果であると考えます。
3 加工・組立系製造業における課題とソリューションの方向性
① 費用削減(製造原価率低減)に向けた課題とソリューションの方向性
加工・組立系製造業においても一般に原材料費が製造原価の構成比率で最も高く、重点対象となります。「使用量削減」については前項で述べましたので、ここでは「単価低減」のソリューションの方向性について述べたいと思います。
加工・組立系の製品(自動車や産業機械など)の多くは、数百から数万点という非常に多くの部品から成り立つ特性があります。一般には製品性能を左右する重要な部品を除いてはサプライヤーから購入し、加工・組立工程で使用されます。単価低減をするためにはサプライヤーからの購買方法をレベルアップさせる必要があります。購買方法は5つの方法で体系化できます(図表6)改善効果の高い方法から述べますと、1つ目は「手配購買」です。いわゆるお願いベースの方法で、こちらの一方的な都合で価格を下げてほしいと要望を出すため、サプライヤーとの関係性を悪化させてしまい、推奨できる方法ではありません。
2つ目の方法は「競争購買」です。複数の候補から相見積もりを取る方法で、ポイントは自社指定の見積もり様式を提示し、横並びで正確に比較をできるようにすることです。
3つ目の方法は「査定購買」です。自社指定の見積もり様式だけでなく、見積りのエビデンスとして、購買品の原価明細(原材料費、労務費、経費の内訳)まで提出を求める方法です。原価をサプライヤーの製造現場で査定したり、類似品の仕様と比較して見積金額の妥当性を論理的に判断することで、単価低減の余地を探る方法です。実施には現場査定やコスト比較をするためのスキルが必要です。
4つ目の方法は「開発購買」です。その名の通り、開発段階からサプライヤーと協業で最低レベルの目標原価を設定・開発する方法です。
5つ目の方法はさらに上流段階から入りこむ「企画購買」です。新素材・新技術の探索から始めて共同開発先を発掘していくアプローチとなります。
② 資産効率化(固定資産回転率向上)に向けた課題とソリューションの方向性
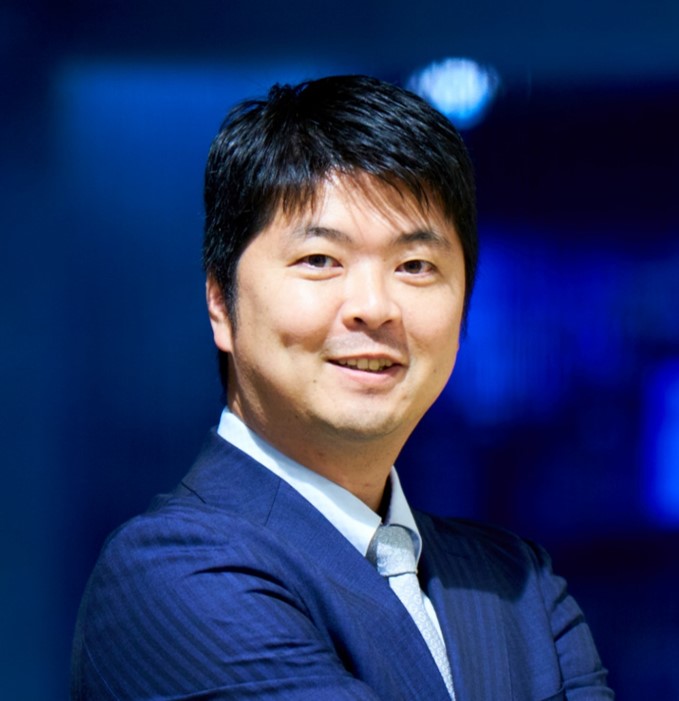
株式会社日本能率協会コンサルティング チーフ・コンサルタント
生産コンサルティング事業本部 生産エンジニアリング革新センター
E-Mail : shinya_yamamoto@jmac.co.jp
経歴
2002年 慶応義塾大学商学部 卒業
2007年 事業会社を経て、株式会社日本能率協会コンサルティング入社
2014年 チーフ・コンサルタント
製造業を中心に 品質、コスト、リードタイムの革新活動、ものづくり人材育成体系構築、生産管理・生産システム構築、
スマートファクトリー構築支援といったコンサルティングテーマで支援をしている。
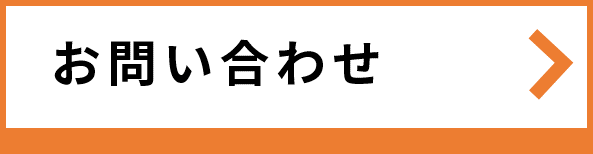